Foundry Tech: Alloy White Irons
In this article, we’ll look at another member of the iron family – Alloy white irons (No, not named after White Industries.). White iron has a white appearance when fractured, just as grey iron has a grey fracture face.
Alloy white irons differ from grey or SG iron; while they have similar carbon contents, the carbon is in solution as carbides, rather than free graphite. Using carbides in combination with nickel and chromium makes these irons very hard and resistant to abrasion.
There are two main groups under the alloy white iron banner, nickel-chromium irons and high chromium Irons.
Nickel-chromium irons were initially produced under the tradename NiHard, but are now covered by various standards. There are two main grades – NiHard 1 and NiHard 4.
NiHard 1 has 5% nickel, 2.5% chromium, and between 3.0-3.6 % carbon. As carbon increases, hardness increases. It has a matrix of martensite (the dark, needle-like phase pictured below), continuous eutectic M3C carbides (as marked) and austenite (the lighter areas). NiHard 1 has abrasion resistance but fracture resistance is not very high. Typical uses in low to medium dynamic stress situations include mixing wheels and blades, grinder components and pump parts.
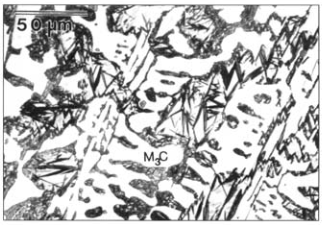
NiHard 1 Microstructure
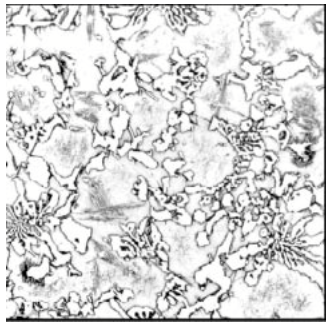
NiHard 4 Microstructure
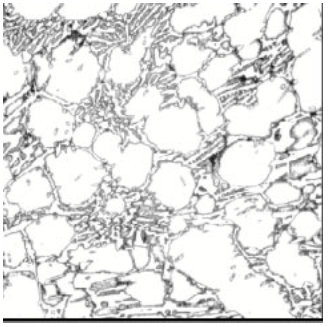
High Chromium Iron
NiHard 4 has 5% nickel, 9% chromium and from 2.5-3.6% Carbon. This alloy has discrete eutectic M7C3 carbides (the isolated light islands in the photo below), martensite and austenite. The discrete carbides improve fracture resistance over NiHard 1. Heat treatment will convert the retained austenite into martensite and secondary carbides, further increasing hardness. NiHard 4 is used in applications such as hammers, blow bars and crushing components where fracture resistance is critical.
High chromium irons have 22-35% Chromium and 2.7-3.2% Carbon, and typically have a matrix of discrete eutectic M7C3 carbides (the isolated light islands in the photo below) and austenite. This can be heat treated to transform the austenite into martensite. These irons are widely used in pumps for corrosive slurries, where impact resistance and abrasion/erosion resistance is essential.